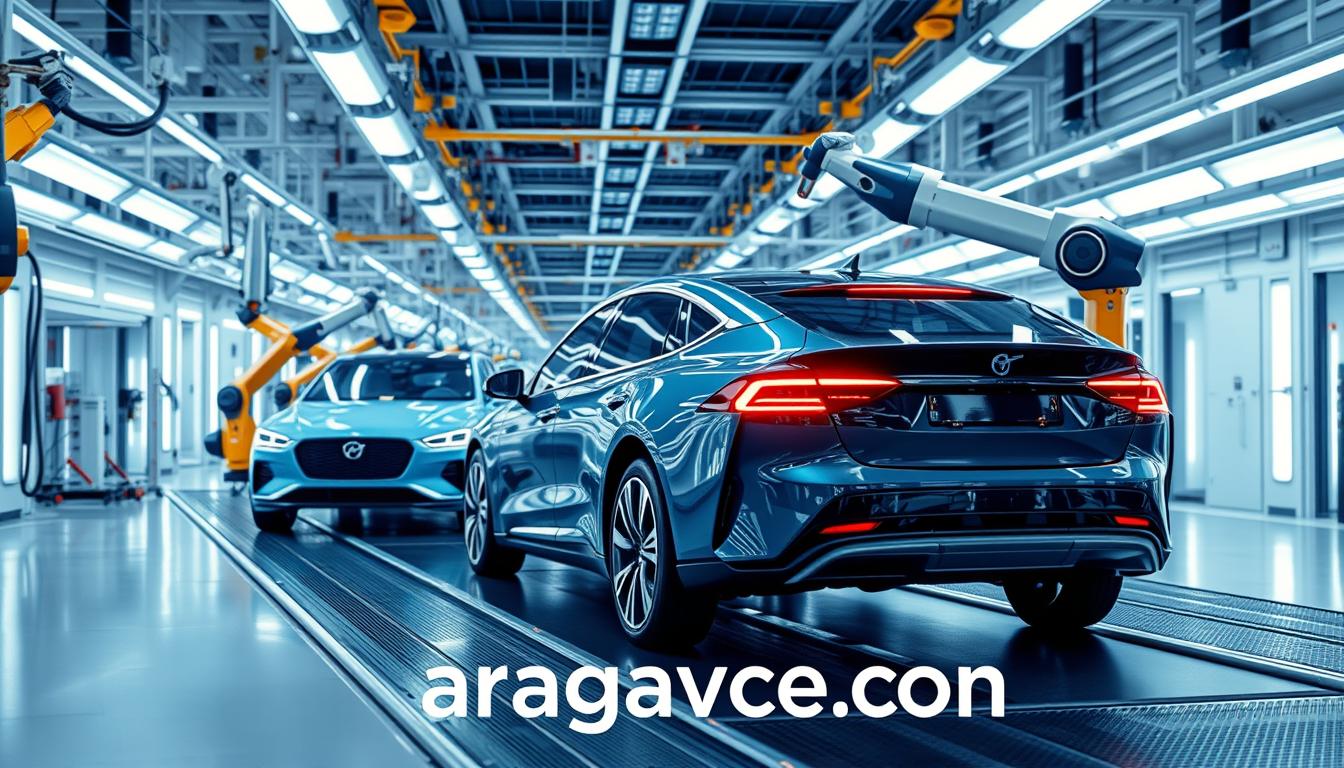
In a world where the automotive landscape is rapidly evolving, one cannot help but ask: Are Korean electric vehicles paving the way for the future of global automotive standards? With the Korean automobile industry’s impressive journey to enhance production capacity and maintain innovative independence, electric car manufacturing has emerged as a critical aspect of this growth. The industry’s ambition reflects an evolving commitment to quality and safety standards that are reshaping electric vehicle production methods globally.
As we delve deeper into this exploration, we will examine how South Korea’s dedicated approach to electric vehicle quality assurance intertwines with its consumer-focused strategies. The anticipated shift towards electric vehicles—expected to constitute 33% of all vehicle ownership by 2040—marks a pivotal change, wherein the industry not only seeks technological advancement but also prioritizes stringent safety protocols and sustainable practices to boost consumer confidence.
Key Takeaways
- The Korean automobile industry has significantly increased production capacity in a short timeframe.
- Indigenous model design has bolstered managerial independence throughout its development.
- Understanding the two coalitions within the industry is essential for grasping its evolution.
- The Korean auto sector’s strategic policymaking has shaped its robust industry structure.
- Electric vehicles are set to transform the market, potentially displacing millions of barrels of fuel daily.
- Growth in electric vehicle sales signifies a profound shift in consumer preferences and industry standards.
- Safety and quality assurance processes are essential drivers of confidence in the electric vehicle sector.
The Evolution of Electric Vehicle Standards
The evolution of Electric Vehicle Standards has significantly shaped the landscape of EV technology. As electric vehicles have gained traction, effective regulations have become essential for ensuring safety and performance. The historical context of electric vehicle safety standards reflects a transition from minimal guidelines to comprehensive frameworks aimed at protecting consumers and enhancing technology.
Historical Context of Electric Vehicle Safety Standards
Initially, the guidelines governing electric vehicles lacked the rigors found in conventional vehicle standards. With the emergence of Electric Vehicle Standards, regulatory bodies started to recognize the unique characteristics of EV technology. Early development relied heavily on less formalized regulations, which evolved as electric vehicles began to capture a more substantial portion of the automotive market. Significant regulations like the Federal Motor Vehicle Safety Standards (FMVSS) laid the groundwork for modern EV Safety Regulations, establishing necessary safety measures to govern battery pack performance and overall vehicle integrity.
Key Regulatory Milestones in EV Manufacturing
Throughout its evolution, the electric vehicle industry has witnessed critical regulatory milestones that have defined manufacturing processes. These milestones include:
- 2010: Introduction of revised FMVSS regulations specific to battery-electric vehicles.
- 2015: Establishment of higher performance standards for EV batteries by organizations such as the Society of Automotive Engineers (SAE).
- 2018: Increased focus on environmental impact led to ASTM International’s initiatives aimed at adapting existing lubricant standards to electric vehicle needs.
- 2020: Global push for stringent safety testing protocols as electric vehicles began to represent a more significant global market share.
As the demand for electric vehicles continues to rise, ongoing evaluations and adjustments of EV Safety Regulations will be necessary to accommodate innovations in technology and manufacturing practices. Understanding this historical context of EV regulations not only highlights past achievements but also prepares the foundation for future advancements in safety and performance.
Understanding the Manufacturing Process of EVs
The manufacturing process of electric vehicles consists of several critical stages that ensure the production of safe, reliable, and high-quality vehicles. EV Manufacturing Processes incorporate various techniques and technologies aimed at achieving optimal efficiency and performance. Understanding these processes offers insight into the industry’s commitment to innovation and quality.
Breakdown of EV Production Phases
The Electric Car Production Phases begin with battery assembly, a cornerstone of EV manufacturing. Lithium-ion batteries, the most prevalent on the market, are produced in three formats: cylindrical, prismatic, and pouch cells. The cylindrical cells have gained popularity due to their balance of energy density and cost. The initial stage involves the creation of electrode sheets, which are coated with a paste that includes materials such as graphite, iron, carbon, and lithium agents. This ensures the cells have the proper electrochemical properties essential for performance.
Methods like winding and Z-folding are employed to stack the sheets, followed by ultrasonic bonding and laser welding to connect the components. Advanced automation in these stages aids manufacturers in maximizing precision and efficiency. Automation directly reduces labor intensity and enhances consistency during production, critical for maintaining the quality of the final product.
Quality Assurance Mechanisms in Electric Car Manufacturing
Quality Assurance in electric car manufacturing involves rigorous inspections and testing throughout the production pipeline. Automated inspection systems, provided by industry leaders such as Cognex and Keyence, play an essential role in gauging and verifying components, especially battery packs. Each battery pack incorporates a Battery Management System (BMS), thermal management systems, and fireproof protection, emphasizing the paramount importance of safety and reliability in EV production.
Attention to quality assurance does not stop at assembly. Multiple charge and discharge cycles are executed during the forming process to pave the way for optimal cell performance. By implementing robust testing protocols, manufacturers can assure customers of the vehicle’s reliability, enhancing consumer confidence in the growing EV market.
Production Phase | Process Description | Technologies Used |
---|---|---|
Battery Assembly | Manufacture of battery cells and modules | Lithium-ion technology, electrode coating |
Electrode Stacking | Creating stacks using winding or Z-folding | Ultrasonic bonding, laser welding |
Inspection and Testing | Quality checks on components and battery packs | Vision systems, automated inspections |
Final Assembly | Integration of battery packs into vehicles | Robotic automation, quality control systems |
Advanced Battery Technology in Electric Vehicles
The landscape of electric vehicles (EVs) is rapidly transforming, driven by advancements in EV Battery Technology. Battery packs serve as crucial components, influencing both performance and overall vehicle efficiency. Innovations in Battery Pack Assembly have become essential to enhance safety, longevity, and affordability of these vehicles.
Innovations in EV Battery Pack Assembly
Recent breakthroughs in Battery Pack Assembly have led to the development of lighter and more efficient battery designs. Manufacturers are focusing on:
- Improved energy density: New battery chemistries, such as lithium-iron phosphate and solid-state batteries, aim to increase the range of electric vehicles.
- Enhanced durability: These advancements ensure that battery packs withstand diverse environmental conditions, promoting longevity and performance.
- Streamlined production processes: Automated assembly lines are becoming commonplace, reducing labor costs and improving assembly efficiency.
As manufacturers adapt to growing consumer demand, understanding these innovations becomes critical in a competitive market. The global acceptance rate of electric vehicles has surged by 43% in 2020, with over 3 million units sold. Projections suggest that by 2030, approximately 30% of all cars will be electric, emphasizing the importance of efficient Battery Pack Assembly methods.
Battery Safety Standards and Compliance
Battery Safety Standards are crucial in addressing the inherent risks associated with electric vehicle batteries. Compliance with these standards is non-negotiable, as they guide manufacturers in developing safe and reliable battery systems. Key aspects include:
- Thermal management systems: Ensuring batteries operate within a safe temperature range between 15°C to 45°C helps to prevent thermal runaway.
- Packaging integrity: Regulations set by bodies such as the National Highway Traffic Safety Administration (NHTSA) focus on the structural design of battery packs to withstand crash conditions.
- Short-circuit prevention: Safety mechanisms to mitigate risks associated with power cells are critical in modern battery designs.
The importance of adhering to Battery Safety Standards cannot be overstated. With safety concerns continuously evolving, manufacturers remain committed to integrating best practices that ensure vehicle reliability and consumer confidence. These efforts underline the necessity for continuous improvement within both EV Battery Technology and overall automotive safety.
The Importance of Safety Standards in EV Production
Safety standards play a crucial role in the electric vehicle (EV) industry, ensuring that vehicles meet rigorous expectations for performance and safety. Electric Vehicle Testing incorporates a variety of assessments, from crash tests to electrical safety evaluations, to establish how well EVs withstand real-world conditions. This comprehensive testing framework is essential for consumer confidence and regulatory compliance.
Overview of Electric Vehicle Safety Testing
Electric Vehicle Testing involves multiple evaluation processes tailored specifically to address the unique challenges posed by high-voltage systems in EVs. For instance, manufacturers design EVs to have insulated high-voltage lines to prevent electrical hazards. Additionally, standards such as the Federal Motor Vehicle Safety Standards (FMVSS) ensure that battery pack performance aligns with safety requirements. For example, FMVSS No. 305 mandates isolation of high-voltage batteries to reduce risk during crashes.
Compliance with National and International Standards
Compliance Standards dictate that commercially available electric-drive vehicles adhere to both national and international regulations. Organizations such as the International Electrotechnical Commission (IEC) and the Society of Automotive Engineers (SAE) have developed guidelines that foster safety and interoperability in the EV market. Standards like ISO 26262 focus on functional safety, while IEC 61851 addresses electromagnetic compatibility to ensure system resilience. Collaboration among manufacturers, governmental bodies, and standard organizations advances the development of these critical guidelines, helping to establish uniform safety protocols that benefit the entire industry.
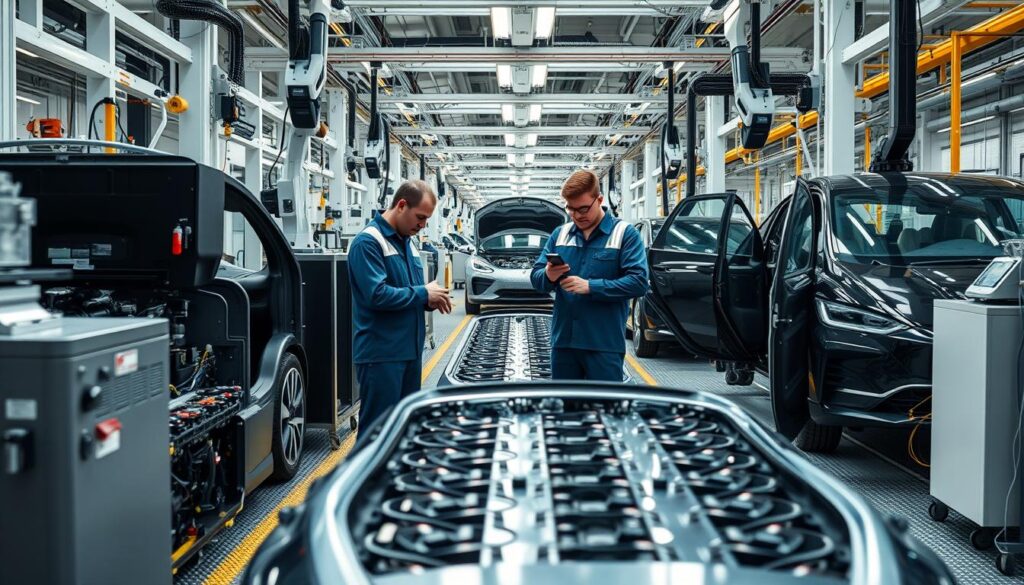
Standard | Description |
---|---|
FMVSS No. 305 | Specifies performance requirements for EV battery packs, ensuring high-voltage batteries are isolated from low-voltage systems during crashes. |
ISO 26262 | Focuses on the safety of automotive systems, including functional safety for electric and hybrid vehicles. |
IEC 61851 | Covers electromagnetic compatibility and interference testing to ensure robust EV systems against electrical disturbances. |
SAE J2990/2_202011 | Adds recommendations for safety systems, including enclosures and identification for high-voltage electrical components in EVs. |
Sustainable Manufacturing Practices in the EV Industry
The push for Sustainable EV Manufacturing has become integral to the electric vehicle sector. As consumer awareness of environmental issues grows, manufacturers are increasingly adopting practices that not only enhance vehicle performance but also prioritize sustainability. Innovations in Eco-Friendly Battery Production and a commitment to minimizing the Environmental Impact EVs have on our ecosystem are at the forefront of this movement.
Innovations in Sustainable Battery Production
Many automakers recognize the need for sustainable battery solutions. Several are focusing on developing batteries with significantly reduced reliance on cobalt and other rare materials. General Motors collaborates with LG to use aluminum instead of cobalt, showcasing a shift to more sustainable materials. Furthermore, Panasonic’s introduction of cobalt-free lithium-ion cells exemplifies a drive towards eco-friendly alternatives that can reduce the cost of electric vehicles by up to 30%.
- Approximately 40% of the value of electric vehicles is attributed to their batteries.
- Sustainable battery innovations can cut lifecycle emissions by nearly 50% compared to their internal combustion engine counterparts.
- Developments like lightweight energy storage components, such as those by Volvo, illustrate the industry’s shift towards environmentally responsible practices.
Reducing Environmental Impact During Manufacturing
To address the Environmental Impact EVs create, the industry is adopting circular economy initiatives. Around 52% of organizations actively promote these concepts, ensuring materials can be reused and recycled. Road traffic is a significant contributor to global CO2 emissions, accounting for one-fifth of the total. Therefore, enhancing manufacturing processes to reduce waste and energy consumption is critical.
Statistic | Value |
---|---|
Consumers willing to change purchasing habits for sustainability | 57% |
Automotive organizations with sustainability strategy | 62% |
OEMs with an electric vehicle plan | 74% |
Growth in electric vehicle sales globally in 2019 | 40% |
Reduction in emissions per car (2005-2018) | 26% |
As the EV industry continues to evolve, it remains crucial to focus on sustainable practices and eco-friendly production methods. These efforts not only contribute to reducing the ecological footprint but also appeal to the growing consumer base that prioritizes sustainability in their purchasing decisions.
Addressing Quality Assurance in EV Supply Chain
The effectiveness of quality assurance processes is vital in the realm of EV production. Manufacturers confront a myriad of challenges, particularly in sourcing high-quality components that align with EV Supply Chain Management standards. Comprehensive management ensures that various parts, especially those integral to the electrical systems and batteries, not only meet strict quality benchmarks but also comply with relevant regulations.
Importance of Supply Chain Management in EV Production
Efficient supply chain management plays a critical role in the EV industry. The shift from traditional Internal Combustion Engine (ICE) vehicles, which typically comprise over 200 parts, to electric vehicles that require only about 20 moving parts signifies a major transformation in production processes. This transition reduces complexity but also demands enhanced oversight in sourcing components, ensuring that each part meets rigorous quality expectations.
- Verification of supplier capabilities is essential, focusing on their commitment to Quality Assurance in EVs.
- Regular audits of suppliers help maintain high standards and foster reliability in the EV supply chain.
- Maintaining close relationships with suppliers can mitigate risks associated with component sourcing, enhancing overall production stability.
Risk Management in EV Component Sourcing
Effective Component Sourcing Risk Management is imperative as manufacturers navigate the complexities of sourcing materials like lithium and cobalt for batteries. The global supply chain faces vulnerabilities, particularly given the average distance battery minerals travel—approximately 50,000 miles from extraction to battery cell production. This extensive travel heightens the risk of disruptions that can significantly impact the availability of critical components.
Risk Factors | Impact on EV Supply Chain | Mitigation Strategies |
---|---|---|
Geopolitical tensions | Disruption in supply of critical minerals | Diversifying sourcing locations and establishing alternative supply channels |
Quality inconsistencies among suppliers | Variability in component performance | Implementing stringent supplier qualification processes |
Environmental regulations | Delays in sourcing due to compliance issues | Proactive engagement with suppliers to ensure compliance |
Human rights abuses in mining | Risk of reputational damage and legal repercussions | Establishing robust ethical sourcing policies |
Consumer Confidence: The Role of Testing and Certification
Consumer confidence plays a crucial role in the adoption and acceptance of electric vehicles (EVs). Robust testing and certification processes significantly enhance buyer trust by demonstrating that vehicles meet necessary safety and quality standards. Without strong consumer confidence, many potential buyers may hesitate due to concerns over battery durability and performance.
How Quality Testing Influences Buyer Decisions
Quality testing impacts consumer decision-making in several ways. A considerable percentage of drivers, around 47%, express concern regarding battery durability. This highlights the necessity for thorough testing to reassure consumers about the longevity and reliability of EV batteries. Furthermore, nearly 56% of drivers mistakenly believe that the range loss from EV batteries is much more severe than reality, indicating a gap in consumer knowledge that effective communication of test results can bridge. Implementing consistent and transparent Consumer Confidence EV Testing results not only informs buyers but also enhances perceptions of reliability and performance among potential customers.
Certification Processes for Electric Vehicles
Certification processes for electric vehicles are critical for establishing trust in the market. In particular, proposals for a standardized battery health certification scheme aim to dispel worries surrounding used electric vehicles. With 82% of all cars sold in the UK in 2021 being in the used car market, the need for credible certification grows. This includes the implementation of battery state-of-health monitors mandated by EU proposals. These efforts are designed to provide essential information to buyers, helping them understand battery health and potential costs associated with replacements. As the market matures, clear EV Certification Processes will not only enhance consumer confidence but will also support the burgeoning second-hand EV market. Here, a detailed overview of the testing and certification landscape can be summarized as follows:
Aspect | Impact | Benefits |
---|---|---|
Battery Health Certification | Increases buyer confidence | Encourages participation in the second-hand market |
Standardized Testing | Reduces uncertainty in EV performance | Improves pricing accuracy |
Transparency of Testing Results | Enhances consumer trust | Encourages informed purchasing decisions |
The Future of Electric Vehicle Manufacturing
The electric vehicle market is evolving rapidly, influencing the future of EV manufacturing. Key factors include the growth in sales and the shift toward low-volume production, promoting flexibility and adaptability. As innovations unfold, industries must consider both emerging trends in EV technology and the adaptation of regulations to maintain safety and quality standards.
Emerging Trends in EV Technology
Recent advancements signal transformative shifts in manufacturing practices. The demand for electric vehicles is driven by numerous emerging trends:
- Automation: The integration of automated processes enhances production efficiency, allowing manufacturers to streamline operations.
- Artificial Intelligence: AI technologies are pivotal for optimizing manufacturing processes, from quality control to supply chain management.
- Sustainable Practices: EV manufacturers are increasingly adopting eco-friendly practices aligned with consumer preferences for sustainability.
- Battery Innovations: With advancements in battery technology, like solid-state batteries, manufacturers can improve performance and safety.
- Low-Volume Production: There is a notable shift toward smaller-scale manufacturing operations, enabling quicker adaptability to consumer needs.
How Regulations Will Adapt to Innovations
The landscape of regulations surrounding EV production is set to evolve alongside technological advancements. As manufacturers innovate, the following regulatory adaptations are expected:
- Safety Standards: New technologies will necessitate updates to current safety standards, ensuring compatibility with cutting-edge innovations.
- Environmental Policies: Regulations will increasingly focus on the environmental impact of EV manufacturing, promoting sustainability initiatives.
- Quality Assurance Protocols: Enhanced quality assurance measures will be critical to uphold standards across the diversified array of new components.
Trend | Description |
---|---|
Automation | Driven by the need for efficiency, automation is becoming a staple in EV manufacturing. |
AI Integration | AI helps improve decision-making and operational efficiency across the supply chain. |
Sustainable Manufacturing | Manufacturers are committed to reducing their carbon footprint through eco-friendly practices. |
Low-Volume Production | Enables quick responses to changing consumer preferences and market demands. |
Innovative Battery Technology | New battery types enhance performance and range, shaping the future of EV usage. |
As the future of EV manufacturing unfolds, it will intertwine emerging trends in EV technology and the adaptation of regulations, ensuring that the industry continues to prioritize safety, quality, and sustainability while meeting consumer expectations.
The Role of Government in EV Production Standards
Government agencies play a pivotal role in shaping the landscape of electric vehicle (EV) manufacturing through a framework of robust regulations. Regulations established by agencies like the National Highway Traffic Safety Administration (NHTSA) directly influence how manufacturers approach EV production. The ongoing evolution of Government Regulations EV Production emphasizes safety, efficiency, and environmental responsibility. In this context, the significant funding from initiatives, such as the Infrastructure Investment and Jobs Act and the Inflation Reduction Act, exemplifies a commitment to bolstering the domestic EV sector.
Governmental Bodies and Their Regulations
Numerous governmental bodies contribute to the establishment of EV Industry Standards, ensuring that manufacturers comply with safety and environmental guidelines. Key highlights include:
- The U.S. Environmental Protection Agency (EPA) aims for 67% of new light-duty vehicles sold to be electric by 2032.
- The Bipartisan Infrastructure Law allocates significant funds for developing EV infrastructure across the nation.
- State legislatures are actively proposing bills, exemplified by New Jersey’s 139 new bills regarding electric vehicles in 2022.
Such initiatives represent a critical infusion of resources aimed at enhancing the EV production landscape and addressing some of the Regulation Challenges faced by manufacturers in terms of infrastructure and technology adaptation.
Challenges in Implementing Effective Standards
While governmental support is substantial, the implementation of effective EV Industry Standards is never without challenges. Key issues include:
- Balancing regulation with innovation, which can often create friction between safety advocates and manufacturers striving for technological advancements.
- Ensuring that funding reaches targeted communities, particularly underserved and rural areas as prioritized in competitive grant programs.
- Adapting existing regulations to accommodate rapid technological advancements in electric vehicles.
In summary, the dynamic interplay between government regulations and the evolving needs of the EV industry highlights the necessity for ongoing dialogue and collaboration among all stakeholders. This collaborative effort aims to create regulatory frameworks that not only promote safety and sustainability but also support innovative growth within the sector.
Regulation Initiative | Funding Amount | Purpose |
---|---|---|
Clean School Bus Program | $2.5 billion | Funding electric school buses |
Bipartisan Infrastructure Law | $5 billion | Building EV charging networks |
Inflation Reduction Act | $370 billion | Climate and energy investments |
The Impact of Emerging Technologies on EV Quality
As the electric vehicle (EV) industry continues to evolve, the integration of emerging technologies plays a crucial role in enhancing overall vehicle quality and safety. The convergence of cutting-edge innovations, particularly in AI in EV production, paves the way for significant advancements. These technologies not only streamline production processes but also ensure that manufacturers can meet rigorous safety standards.
Next-Gen Technologies Enhancing Safety and Quality
Next-Gen safety technologies are effectively addressing the complexities of modern EV manufacturing. These improvements focus on predictive maintenance and automated quality checks that minimize human error while maximizing efficiency. The following key developments showcase how these technologies elevate the quality of EVs:
- Predictive Analytics: Anticipates potential failures and maintenance needs through data analysis.
- Automated Quality Assurance: Software solutions conduct real-time assessments during production to ensure adherence to standards.
- Advanced Driver Assistance Systems (ADAS): Incorporates safety features such as lane-keeping assistance, collision avoidance, and adaptive cruise control.
The Intersection of AI and EV Manufacturing
The intersection of AI and EV manufacturing has sparked a transformative era in production techniques. Automation and machine learning enable efficient supply chain management and enhance product reliability. Key benefits of AI in EV production include:
Technology | Benefit | Impact on EV Quality |
---|---|---|
AI-Powered Robotics | Reduces assembly line errors | Increased accuracy and precision |
Data-Driven Manufacturing | Improves resource allocation | Optimized production costs and time |
Real-Time Monitoring Systems | Immediate problem identification | Enhanced safety protocols and risk management |
As the industry moves forward, the commitment to integrating these emerging technologies in EV manufacturing signifies a brighter, more sustainable future. Embracing innovations such as AI and next-gen safety technologies will set new benchmarks for quality and consumer confidence in electric vehicles.
Conclusion: Embracing Quality and Safety in EV Manufacturing
As the electric vehicle industry continues to thrive, a firm commitment to safety and quality innovations in EVs has become increasingly essential. The progress made in manufacturing processes, driven by technological advancements and stricter regulations, has laid vital groundwork for consumer confidence and market acceptance. With over 275,000 plug-in electric vehicles (PEVs) currently cruising the streets of the United States, the demand for reliable and safe electric vehicles has never been clearer.
Summary of Key Safety and Quality Innovations
The journey toward improving electric vehicle standards is underscored by several key innovations. From advancements in battery technology that address performance and safety challenges to rigorous compliance with international regulations, the industry is climbing towards higher benchmarks. The need for effective quality assurance measures has become critical as the number of electric vehicles rises, matching consumer expectations while addressing lingering concerns regarding infrastructure and charging capabilities.
Future Directions for EV Quality Standards
Looking ahead, the future directions in EV standards will likely encompass not only enhancements in safety protocols but also a more robust focus on sustainable practices. As global markets shift, manufacturers must navigate a landscape characterized by emerging technologies and increased regulatory scrutiny. Continually adapting to these changes will ensure that electric vehicles not only remain competitive but also contribute positively to our evolving urban environments, paving the way for smarter, more efficient transportation solutions.
FAQ
What are the most important safety standards for electric vehicles?
Electric vehicles must comply with various safety standards, including the Federal Motor Vehicle Safety Standards (FMVSS) and guidelines set by the National Highway Traffic Safety Administration (NHTSA). These standards cover critical aspects such as battery performance, crash safety, and electrical system integrity.
How does the manufacturing process for electric vehicles differ from traditional vehicles?
The manufacturing process for electric vehicles (EVs) involves unique phases such as battery pack assembly, electric motor production, and powertrain integration. The focus is on quality assurance and rigorous testing to ensure safety and reliability in the final product.
What role does battery technology play in electric vehicle manufacturing?
Battery technology is crucial for electric vehicles as it directly impacts vehicle performance, range, and safety. Innovations in battery chemistry and packaging are continually being developed to enhance lifecycle, efficiency, and crash safety of EV battery packs.
How do manufacturers ensure the quality of components in electric vehicle production?
Manufacturers conduct stringent risk management strategies, supplier audits, and comprehensive quality assurance practices to ensure that components meet regulatory compliance and quality standards throughout the supply chain.
What sustainability practices are becoming common in electric vehicle manufacturing?
Many electric vehicle manufacturers are implementing sustainable practices such as recycling battery materials, utilizing energy-efficient production methods, and reducing waste in their manufacturing processes to align with environmental sustainability goals.
How do testing and certification influence consumer confidence in electric vehicles?
Rigorous testing and certification from recognized organizations enhance consumer trust, by demonstrating that electric vehicles meet established safety and quality standards. A robust certification process assures buyers about the vehicle’s reliability and safety.
What emerging technologies are impacting electric vehicle manufacturing?
Emerging technologies like artificial intelligence and machine learning are enhancing the EV manufacturing process by enabling predictive maintenance, real-time monitoring, and automated quality checks, thus improving overall safety and efficiency in production.
What challenges do government regulations present to electric vehicle manufacturers?
Manufacturers face challenges in navigating the evolving regulatory landscape, as they must balance innovation with the need for safety. Ongoing collaboration between government agencies and manufacturers is essential for developing effective standards that address these challenges.